Specification
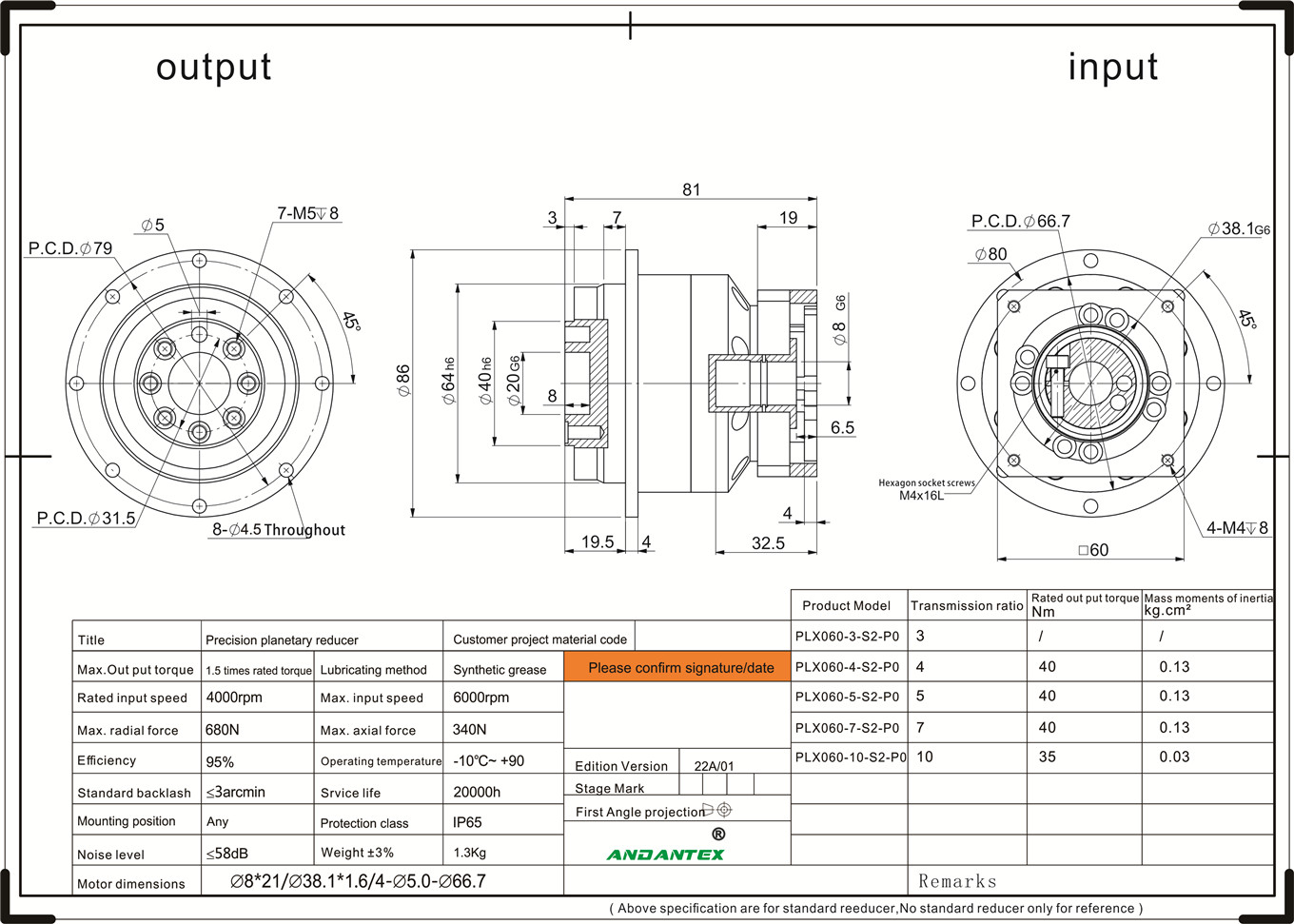
Features
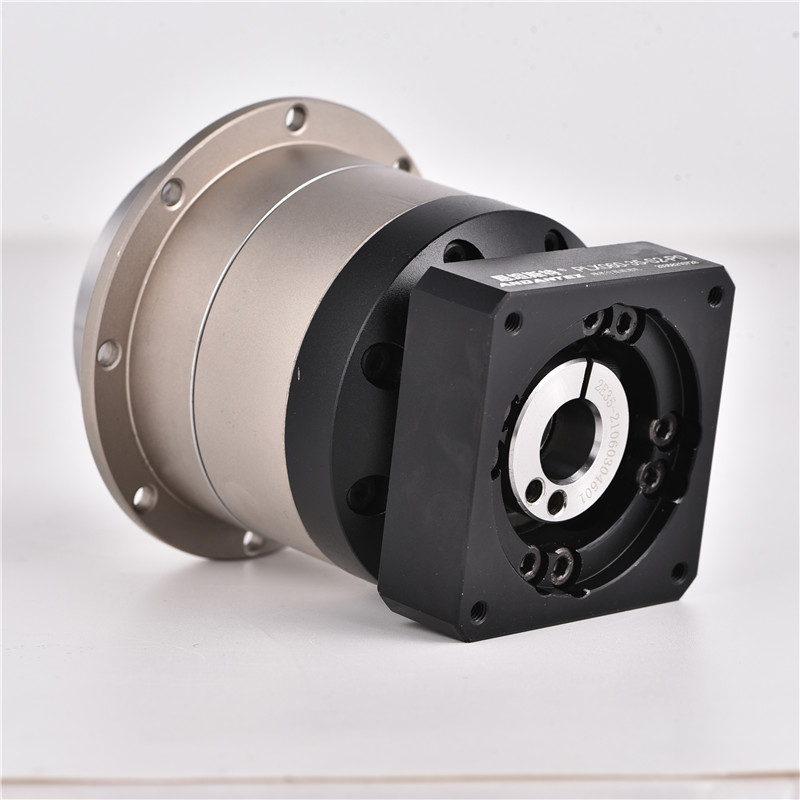
A high-precision disc reducer is a mechanical device specifically designed to convert the high rotational speed of an electric motor into a low-speed, high-torque output. Its core structure consists of a disk and a series of gears, and it typically features high-precision ratios and a small footprint for a variety of industrial applications. The design of the device allows for high performance power transmission in a small space and is an integral part of modern machinery and equipment.
Applications
In mechanical equipment, the role of high precision disk reducer cannot be underestimated. First, it plays a key role in automation equipment. With the rise of intelligent manufacturing and Industry 4.0, automated production lines are being commonly used in various industrial fields. High-precision disc reducers provide precise motion control and positioning for these devices, ensuring stable operation and high efficiency. For example, in automated assembly lines, gearboxes enable precise component positioning, improving overall production efficiency and product consistency.
Industrial robots are another important application area for high-precision disk reducers. In a variety of industrial operations, such as welding, handling and assembly, the gearhead becomes a core component of the robot's motion system by converting the high-speed rotation of the motor into a low-speed, high-torque output. It enables the robot to perform complex operations with high precision and stability, thereby improving the automation of the production process and product quality. In addition, the reliability and durability of the gearbox guarantees the long-term stable use of industrial robots, which is crucial for modern manufacturing.
In the example below, a 400W servo + PLF series gearbox is used. When the operating inertia is too large, the gearhead is easily damaged.
Problem 1: The motor is not able to output the required torque in a very short period of time.
Problem 2, the PLF series can't withstand such a large inertia causing the gears to break.
3, the clearance during operation is very large. The motor shakes abnormally. There is no way to reach the specified position accurately.
Solution:
1, replace PLX090 reducer + 750W servo motor, increase the reduction ratio. Increase the inertia.
2, use NT130 hollow rotary stage + 400W servo motor. Smooth operation and increased precision.
3, Use NT200+1000W servo motor. Without any risk. Precision and torque are maximized. It is a very insurance solution. Our engineers recommend the third solution.
Package content
1 x pearl cotton protection
1 x special foam for shockproof
1 x special carton or wooden box
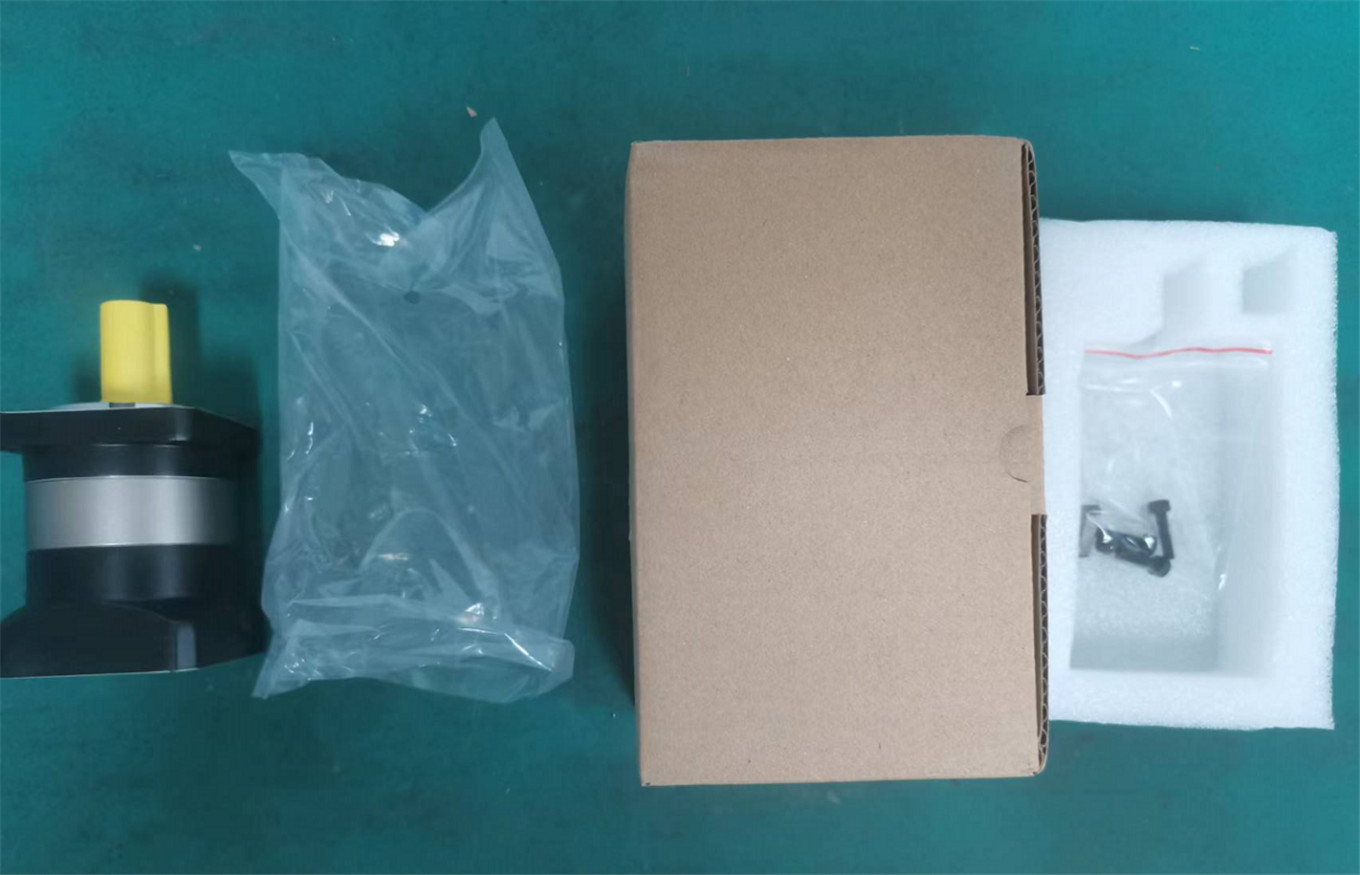